How to Solve Warranty Problems Today
First horse out of the gate: REDESIGN. Or is it? To start with, I need to remind you to be extremely careful not to automatically think “Redesign,” when you start having warranty problems. [bctt tweet=”“You can always redesign, but redesigns are not only expensive, they also introduce new problems.”” username=”@lightningsolve”]
You can always redesign, but redesigns are not only expensive, they also introduce new problems. With a little investigation, usually you’ll find a root cause that saves you from needing to redesign. So listen up, Gumshoe! Sleuthing saves you money.
I’m ready to Investigate our Warranty Problem Intelligently instead of Resorting to Redesign. Where do I start?
Good question! Every successful jockey gets some expert training under his belt before jumping on Secretariat’s back. You’re in luck – training is one of the things I do best! This blog is similar to my video entitled, “Broken Parts, 5 Steps to Solve FAST,” with a few exceptions. Warranty problems normally take a longer time to address because it’s harder to find good parts to compare to the broken ones. [bctt tweet=”“Warranty problems normally take a longer time to address because it’s harder to find good parts to compare to the broken ones.”” username=”@lightningsolve”]
What are some Good Part Characteristics?
In order to find a good part, you need to find some parts that have been in the field for a very long time and have not broken yet. Also, if you know the environment that the warranty parts are from, it’s best to find good parts that are also from that environment. For example: if your warranty problem has to do with rust, then try to find a good part from a corrosion state. Because this can be difficult, in general, I only like to give warranty projects to Master Problem Solvers. [bctt tweet=”“Because this can be difficult, in general, I only like to give warranty projects to Master Problem Solvers.”” username=”@lightningsolve”]
Now you’re going to want 5 good parts to compare to 5 warranty return parts. Compare the good with the bad, looking for any kind of contrast. Contrast makes the world go round! It is a positive find in this line of work.
Now for the Really Aggravating Part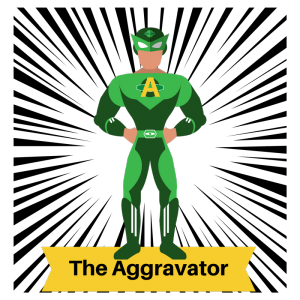
The next step is to reproduce the event. Often you need to find an Aggravator. But, just like in real life, you have to be careful with them. Aggravators can be very risky, because you need to take special care to make sure your artificially aggravated parts fail just like the warranty return parts.
Once you have successfully reproduced the event, and you know what’s different between the good parts and the bad parts, you’re ready for the next step. Confirm you have root cause by making 3 new parts the good way, and 3 new parts the bad way. If the 3 bad ones fail and the 3 good ones do not fail, then congratulations! Most likely you have found your root cause! Happy Dance Time!! [bctt tweet=”“Just because warranty projects are hard, it does not mean they are impossible. Don’t hesitate to call a warranty problem solving expert if you need help.”” username=”@lightningsolve”]
Call for Reinforcements
Just because warranty projects are hard, it does not mean they are impossible. A warranty problem solving expert can save you time, money, and the headache of dealing with the new problems that will inevitably arise from a redesign. A good one will make sure your problem is solved the right way, quickly! Never hesitate to call an expert if you need help.
I would love to learn from your experience too! Please share in the comments below any extra pointers you have for solving warranty projects lightning fast!